Company
Hankook Tire develops ‘Damaged Parts Restoration 3D Printing Technology’ with Korea Atomic Energy Research Institute
2023. 01. 19
- Hankook Tire joins hands with Korea Atomic Energy Research Institute to develop additive restoration technology
for metal 3D printing
- Aims to improve economic efficiency and decrease carbon emissions by reducing unnecessary consumption of
materials and costs
Seoul, Korea, January 19, 2023 – Global leading tire company Hankook Tire & Technology has developed ‘Damaged Parts Restoration 3D Printing Technology’ through research collaboration with Korea Atomic Energy Research Institute and HM3DP, a 3D printing startup.
The Damaged Parts Restoration Technology is a spin-off, a technology in one specific field that leads to a development of technology in other fields, of an additive manufacturing process through 3D printing technology originally developed for high performance components for nuclear reactors. The identical technology can now be applied to restore special metallic parts in non-nuclear industries.
Researchers from Hankook Tire’s central research center, Hankook Technodome, and Korea Atomic Energy Research Institute have successfully restored damaged parts of Titanium (Ti) alloy blades in Hankook Tire production lines using the Directed Energy Deposition (DED) method. The blades are used to repeatedly cut tire rubber materials which contain a significant amount hardening agents.
Prior to the development of this technique, Hankook had to inevitably discard worn or damaged Ti alloy blades after it was used. The innovative Damaged Parts Restoration Technology enables Hankook to repair them for reuse, reducing material consumption and increase cost efficiency as Ti alloy blades cost significantly more than those of stainless steel.
Through the implementation of this technology, Hankook Tire has also made a significant contribution to creating an eco-friendly, carbon-reducing parts manufacturing industry, contributing to the company’s corporate social responsibility by reducing carbon emissions generated during parts manufacturing. The blades, which were repaired using the additive 3D printing technology, are currently installed and are under verification at the production facilities in Hankook Tire’s Daejeon plant.
Hankook Tire has been continuously developing the innovative and potent 3D printing technology by proactively introducing industrial metal 3D printers in 2015 to find best way to realize innovation and even completed a serial production system of 3d sipes - tire mold that engraves fine patterns on tires, for the first time in Korea. The company plans to continue collaborating with domestic and foreign experts to achieve the technological innovation of the cutting-edge manufacturing technology of 3D printing.
Meanwhile, Hankook Tire is continuously seeking for innovation through collaboration in various fields. The company has teamed up with KAIST (Korea Advanced Institute of Science and Technology) for joint research on future technologies and industry-university cooperation to improve digital technology capabilities and innovative R&D through Digital Transformation. It also carried out a cooperative development project, Road Hazard Prediction & Detection Solution, with SK Planet to preemptively respond to potential hazards by identifying road conditions through artificial intelligence and deep learning technology.
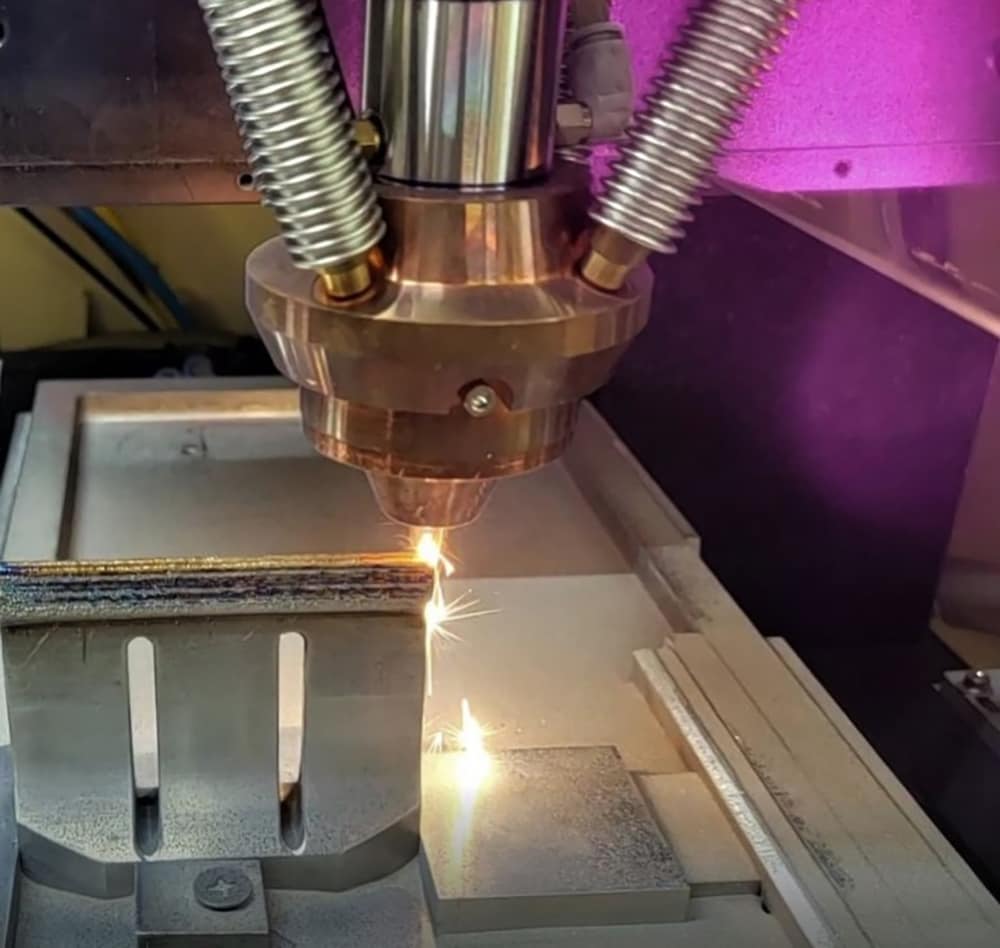
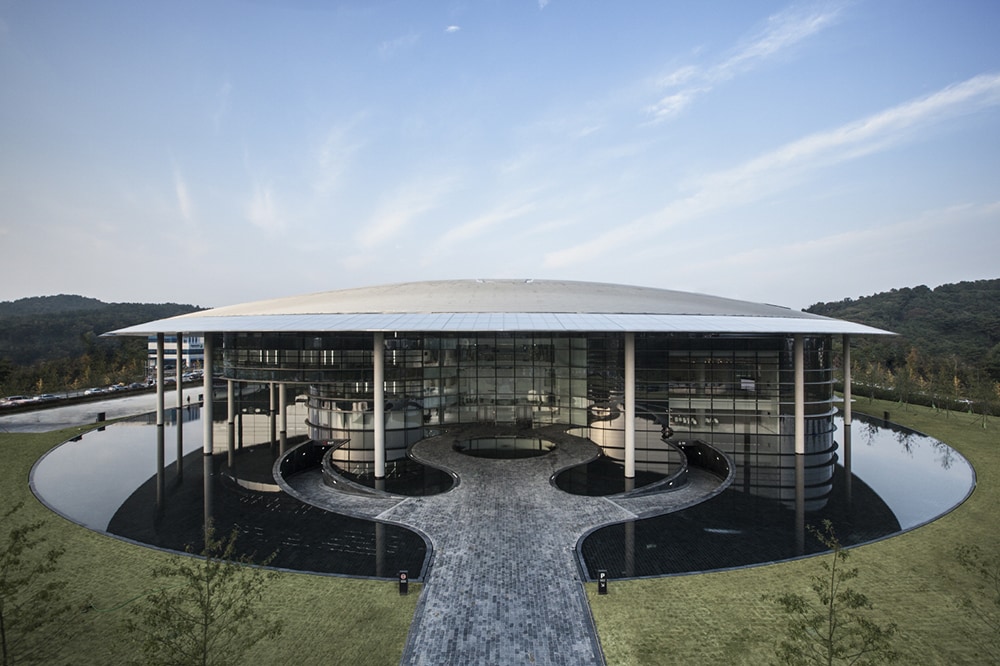